Conveyor Rollers: A Comprehensive Guide
Conveyor rollers, as essential components of conveyor systems, are designed to support conveyor belts and their loads, ensuring smooth and efficient material transportation. The type and model of a conveyor roller vary depending on the specific application, material characteristics, and conveying requirements. This article will delve into the classification, structural features, applications, and maintenance of conveyor rollers.
Classification of Conveyor Rollers
Based on their structure and function, conveyor rollers can be categorized as follows:
- Troughing Rollers: Composed of three sets of rollers arranged in a “V” or “U” shape to support the concave portion of the conveyor belt. Commonly used for conveying bulk materials in mining, metallurgy, and coal industries.
- Parallel Rollers: Featuring a flat surface, these rollers support the lower plane of the conveyor belt. Widely used for conveying packaged or boxed goods in logistics, warehousing, and light industries.
- Impact Rollers: Covered with rubber rings to cushion the impact of falling materials onto the conveyor belt. Installed at the discharge point of conveyors, they are suitable for conveying heavy or impact-prone materials.
- Self-aligning Rollers: These rollers can automatically adjust to correct belt misalignment. They are flexible in design and suitable for long-distance conveying systems to ensure stable operation.
- Friction Rollers: With a specially designed friction surface to increase friction between the roller and the conveyor belt, preventing slippage. Often used in wet or slippery conditions, or where additional friction is required.
- Spiral Rollers: Featuring a spiral surface, these rollers have a self-cleaning function, effectively removing material residue from the conveyor belt. Suitable for conveying powdery or sticky materials, reducing belt contamination.
- Conical Rollers: Tapered at both ends, these rollers are used at conveyor belt turning points to ensure smooth transitions. Commonly used in curved conveyors and special process lines.
Key Technical Parameters of Conveyor Rollers
- Diameter: Typically ranging from 50mm to 219mm, the diameter is selected based on the conveyor belt width and material weight.
- Length: Generally the same as the conveyor belt width, commonly ranging from 800mm to 2400mm.
- Material: High-quality carbon steel, stainless steel, or engineering plastics are commonly used to meet various working conditions.
- Sealing performance: High-quality rollers feature multiple sealing structures to prevent dust and water, ensuring operation in harsh environments.
Installation Requirements for Conveyor Rollers
- Spacing: The installation spacing of rollers should be determined based on factors such as material weight and conveyor belt tension, typically ranging from 500mm to 1500mm.
- Levelness and straightness: Rollers must be installed horizontally and in a straight line to prevent belt misalignment and uneven stress.
- Lubrication and maintenance: Regular inspection and lubrication of roller bearings are essential to ensure smooth rotation and extend service life.
Application Areas of Conveyor Rollers
- Mining and coal industries: Conveying bulk minerals, coal, and other materials, often using troughed and impact rollers.
- Ports and terminals: Used in bulk material handling systems for long-distance, heavy-duty conveying.
- Logistics and warehousing: For light-duty conveyor systems, often using parallel and self-aligning rollers.
- Cement and chemical industries: Conveying powdery, sticky, or corrosive materials, often using spiral rollers and corrosion-resistant materials.
Future Trends in Conveyor Rollers
- High-performance materials: Incorporating high-strength, lightweight materials such as engineering plastics and composites to reduce energy consumption and extend service life.
- Intelligent design: Integrating sensor technology to monitor the operating status of rollers in real-time, improving the automation level of conveyor systems.
- Environmental friendliness: Adopting low-noise designs and environmentally friendly materials to meet the needs of industrial environmental protection.
Conclusion Conveyor rollers, as critical components of conveyor systems, significantly impact the efficiency and reliability of material transportation. The selection and application of appropriate roller models based on specific working conditions are crucial for ensuring the stable operation and maximum economic benefits of the equipment. If you require roller selection advice or customized services, please feel free to contact our technical team.
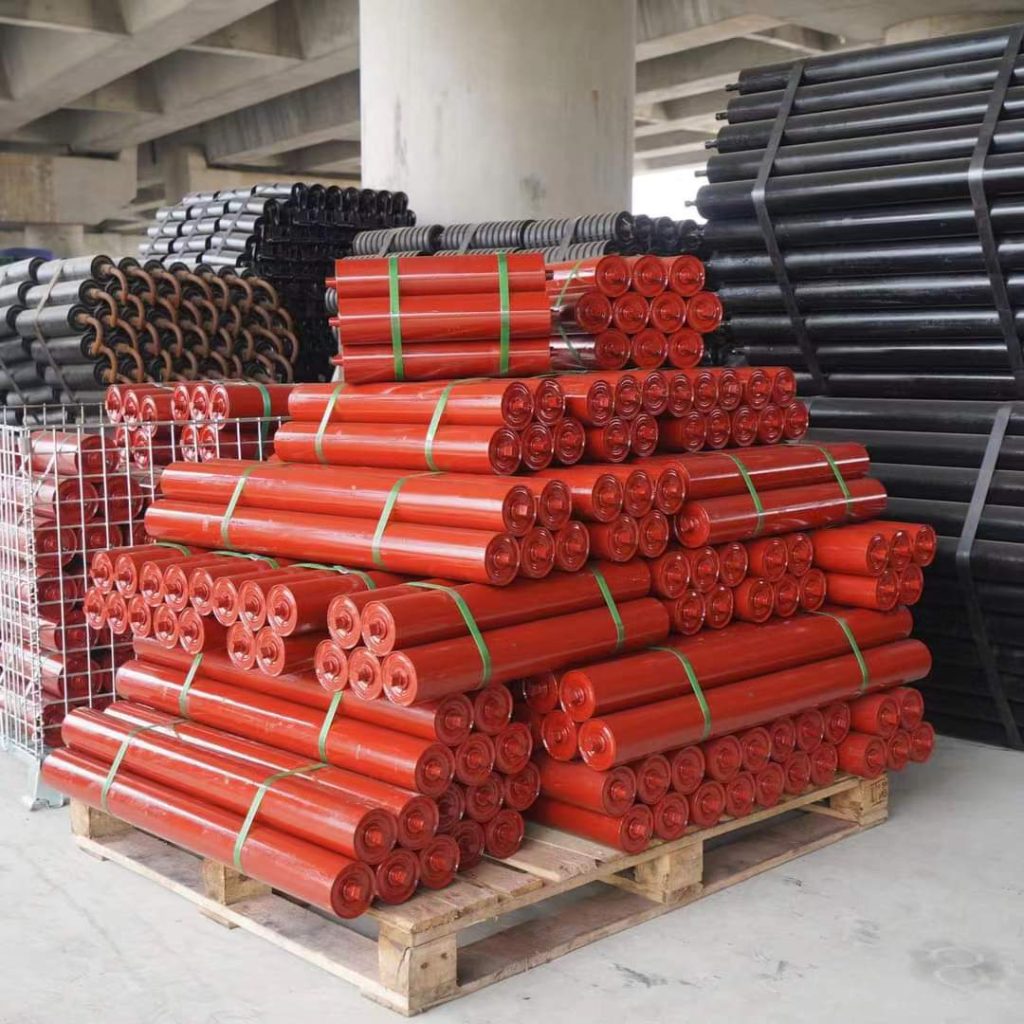