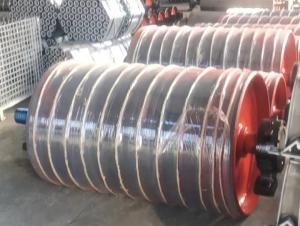
Conveyor Rollers: The Backbone of Conveyor Systems
Conveyor rollers are essential components of conveyor systems, playing a crucial role in supporting conveyor belts and ensuring smooth material transportation. This article will delve into the various types, structures, materials, applications, and maintenance procedures of conveyor rollers.
Classification of Conveyor Rollers
Conveyor rollers can be categorized based on their structure and function:
- Parallel Rollers: These have a flat surface and support the lower plane of the conveyor belt, widely used for conveying boxes, pallets, and other items.
- Troughing Rollers: Featuring a V-shaped or U-shaped profile, they support the concave portion of the conveyor belt, primarily used for conveying bulk materials.
- Impact Rollers: Covered with a rubber layer to cushion impacts, they are suitable for conveying fragile items or reducing shock.
- Self-aligning Rollers: Designed to automatically correct belt misalignment, ensuring stable operation.
- Drive Rollers: Powered by a motor to drive the conveyor belt.
- Idler Rollers: Used to change the direction of the conveyor belt.
- Spiral Rollers: With a spiral surface, they have self-cleaning properties and are suitable for conveying sticky materials.
Structure of Conveyor Rollers
A typical conveyor roller consists of a shaft, body, bearings, and seals.
- Shaft: Provides support and connects the roller to the drive mechanism.
- Body: The part that comes into contact with the conveyor belt, made of various materials based on the application.
- Bearings: Reduce friction and ensure smooth roller rotation.
- Seals: Prevent dust, water, and other contaminants from entering the bearings, extending their service life.
Materials Used for Conveyor Rollers
- Carbon Steel: Widely used, cost-effective, but susceptible to rust.
- Stainless Steel: Offers excellent corrosion resistance, suitable for harsh environments.
- Cast Iron: Provides good wear resistance, often used for heavy-duty applications.
- Plastics: Lightweight and corrosion-resistant, commonly used in the food and pharmaceutical industries.
Applications of Conveyor Rollers
Conveyor rollers find extensive applications in:
- Logistics: Conveying packages, goods, etc.
- Food industry: Conveying food ingredients, finished products, etc.
- Mining: Conveying ores, coal, etc.
- Port terminals: Conveying bulk materials.
Maintenance and Care
Regular maintenance is essential to ensure the optimal performance of conveyor rollers. This includes:
- Inspection: Regularly check for wear, cracks, and other damage.
- Lubrication: Periodically lubricate bearings.
- Cleaning: Clean the roller surface to remove dust and debris.
- Adjustment: Regularly check and adjust roller spacing and levelness.
Future Trends
- Intelligent: Incorporating sensors for real-time monitoring of roller operating conditions.
- Modular: Adopting modular designs for easy installation and maintenance.
- Eco-friendly: Using environmentally friendly materials to reduce environmental impact.
[Insert the image of a conveyor roller here]
Image Caption: A typical conveyor roller, showcasing its robust construction and various components.
Note: To provide a more comprehensive understanding, consider adding diagrams or illustrations to visually represent the different types of conveyor rollers and their components. Additionally, you might want to include information about specific applications, such as rollers used in automated warehouses or industrial production lines.
Would you like me to add more details or create a more specific article based on your needs?